Insulating A Listed Building’s Walls
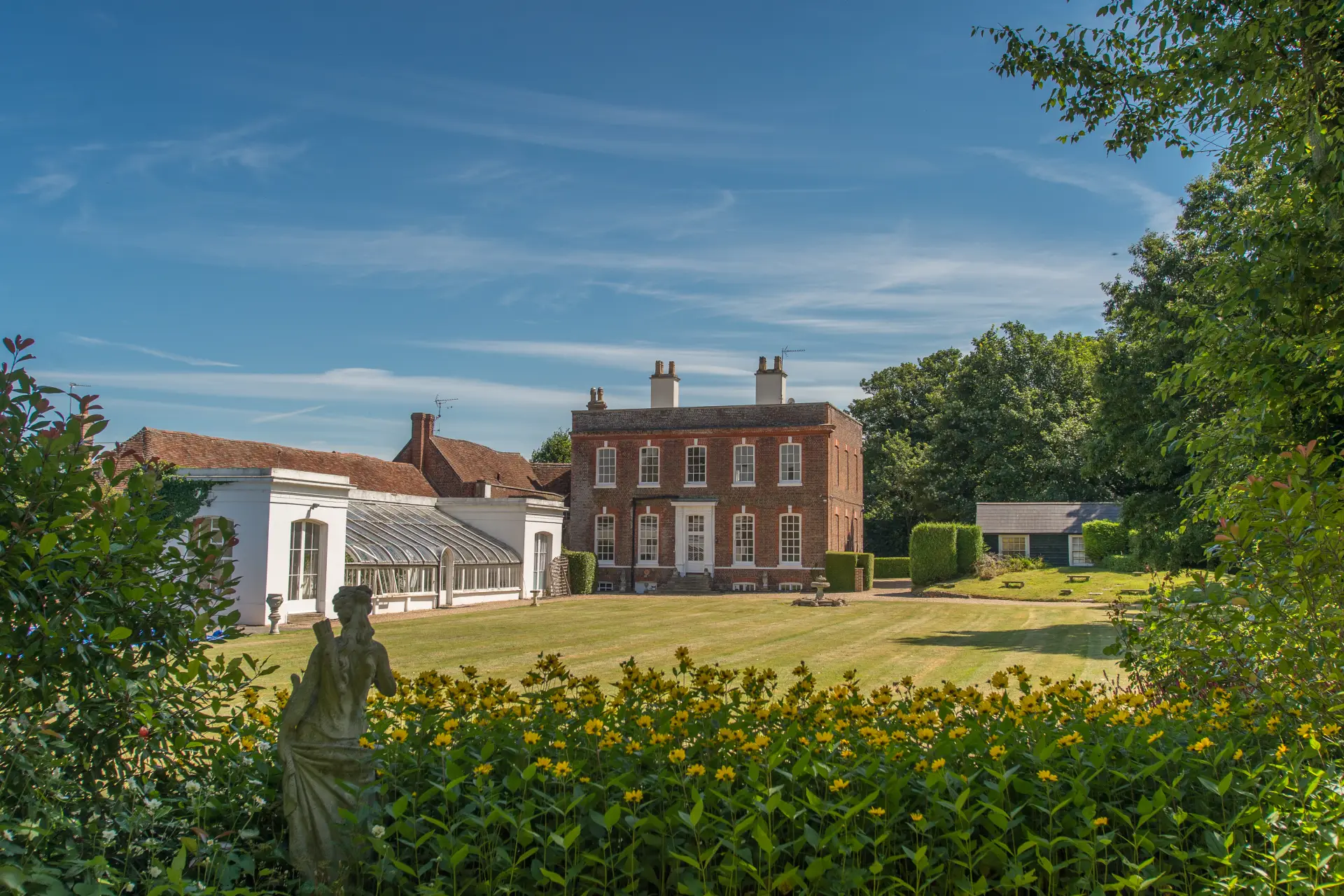
Improving Listed Building Wall Insulation
Insulating a listed building can make the structure more energy efficient by creating a drier and warmer environment with adequate airflow. This helps preserve historic fabric, including timbers and render, which in turn reduces maintenance costs. But can you insulate the walls of a listed building?
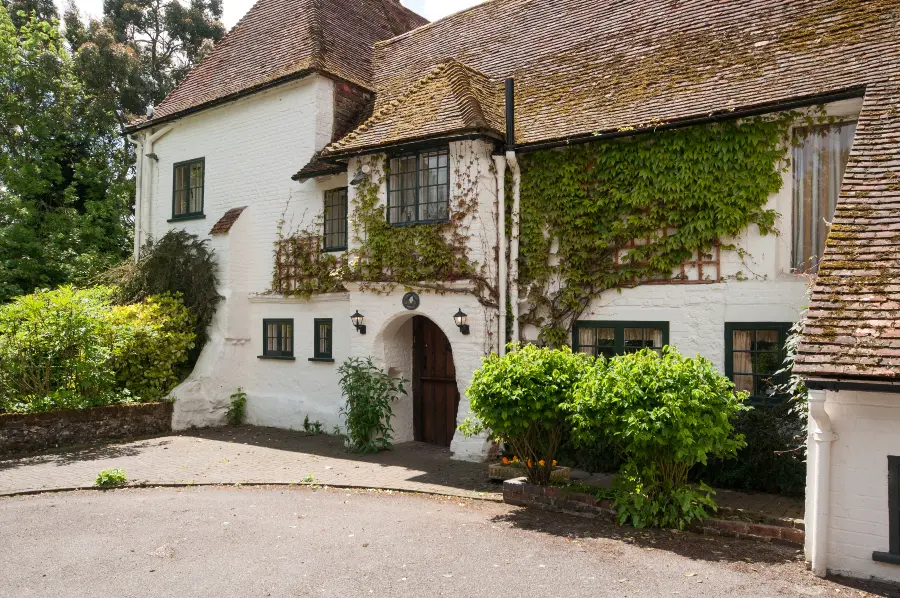
In principle, adding insulation to a listed building is possible and can be effective; however, it’s a complicated process. Installing wall insulation in historic structures requires meticulous design and detailing, appropriate choice of materials, and high workmanship standards. Well-intentioned work carried out by non-specialised builders can create new technical risks, such as condensation, which leads to mould and decay.
Heritage and conservation specialist, Anske Bax, has years of experience helping listed building owners successfully improve the thermal performance of their homes. Below, he discusses the best strategies for insulating a listed building’s walls.
Factors To Consider When Deciding How To Insulate A Listed Building
When it comes to improving the energy efficiency of a listed building, there are many factors to examine, such as:
- The building’s heritage value and its context,
- Original construction materials and techniques,
- Thermal mass,
- Breathing performance,
- Existing damp and wall condition,
- Hygrothermal behaviour,
- Environmental influences, and
- Local wildlife.
Only a specialist architect can correctly weigh these factors to devise suitable techniques and materials. When analysing the options available to you, the specialist will also assess the cost, speed, and effectiveness of suitable techniques and materials. They will then need to work with specialist builders experienced in working on historic buildings.
Do I Need Listed Building Consent To Insulate A Listed Building?
Before adding any insulation to a listed building, you need to gain listed building consent from the Local Planning Authority (LPA). If the building is in a conservation area or a national park, or if you plan to make significant alterations - such as adding non-matching external insulation - you will also need to apply for planning permission.
The LPA will set a schedule of works for repair and methodology and provide a condition of listed building consent, which specifies a required mix of materials you will need to use for the work.
Anske recommends investing in thermal upgrading when your listed building requires maintenance. For example, if you need to replace poor-condition render or cladding, you have an opportunity to add insulation panels under it. Installing insulation while carrying out regular maintenance will lower the cost of the works and increase your chance of gaining listed building consent.
Insulating Solid Walls
Insulating traditional solid walls is often challenging and costly; however, in some cases, it’s worthwhile - especially if done as part of regular maintenance.
Adding External Insulation To Solid Walls
Insulation, such as mineral wool and wood-fibre panels, can be added to exterior sold walls and covered with a moisture-permeable like-for-like finish. This increases wall thickness, which means you likely need to relocate windows and doors further forward and adapt the roof and wall junctions.
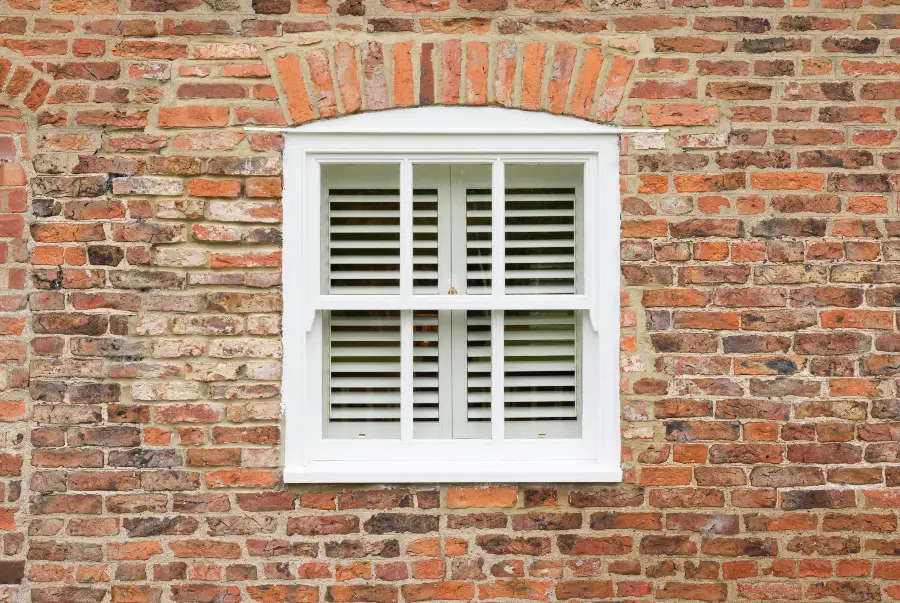
External insulation fundamentally changes a structure’s appearance, even if it’s already rendered, so, according to Anske, it’s rarely approved for use in listed buildings.
Adding Internal Insulation To Solid Walls
Internal insulation is applied to the inner face of a wall. Anske recommends using breathable materials, like 12mm natural cork sheet lining and Thermafleece lamb’s wool insulation. A matching finish is then applied to the room side. It’s worth bearing in mind that internal insulation reduces the size of a room.
Obtaining permission for internal insulation is possible if the interior wall isn’t especially significant and if the plan is part of a well-designed thermal upgrading scheme. Your proposal will need to outline the replication, like-for-like, of any significant internal features - such as plaster cornices - and joinery components, such as door architraves.
Timber-Framed Walls
Timber-framed buildings date back to Medieval, Roman, and Georgian times. They have highly sensitive and rare fabric and finishes, which need special protection. The integrity of the timber affects a building’s structural performance: if a single timber joint fails due to rot and decay, the frame can become distorted and parts of the building can fail.
Improving the energy efficiency of a timber-framed building is often too costly to justify. However, regular maintenance often offers a cost-effective opportunity to install wall insulation.
Suitable materials for improving the thermal performance of a timber-framed building include:
- Wood-fibre board,
- Sheep’s wool batts,
- Hemp-fibre insulation boards,
- Flax-fibre batts,
- Cellulose fibre.
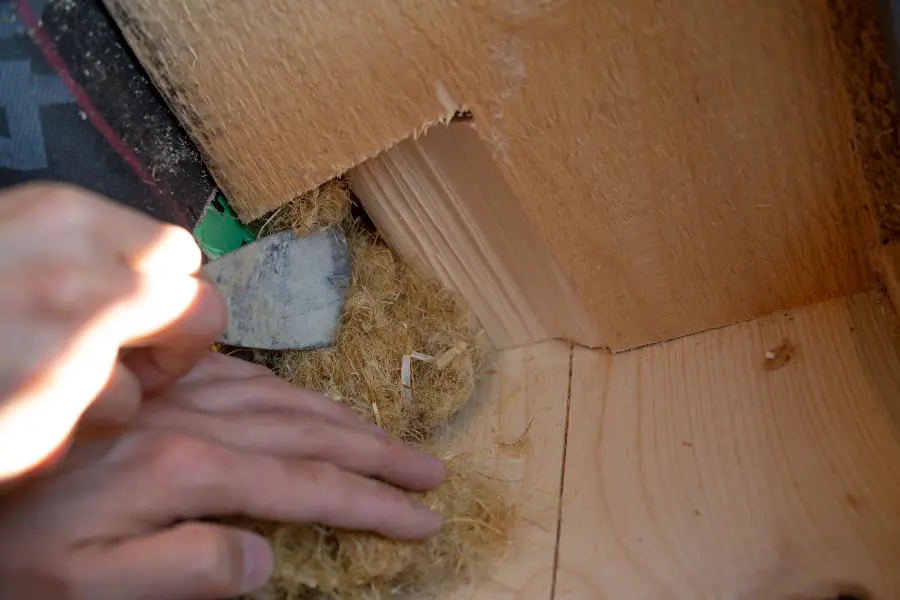
Anske usually recommends using wood board batts made of cork because they are easy to obtain, cheap, and efficient. However, bear in mind that, with listed building insulation, choice of materials is always set on a case-by-case basis.
Replacing Impermeable Materials Used For Repairs Of Timber-Frame Walls
If impermeable materials, such as cement-based renders, have been used to repair a timber-framed building in the past, its thermal performance has been negatively affected. Replacing these materials with breathable ones helps. This is an effective intervention that’s worth adding to a maintenance plan or thermal upgrading package.
Adding External Insulation To Exposed Timber Frame Walls
Enhancing the thermal performance of buildings with exposed timber frames and infill panels is challenging. In Anske’s experience, installing external insulation under a breathable membrane is easy to do and cost-effective. Using this technique will likely help gain listed building consent.
Gap Filling In Timber Frame Walls
Timber-frame buildings often have gaps and cracks between the frame and infill panels, which create draughts. Filling these gaps with a traditional heritage putty is a cost-efficient and effective way to improve energy efficiency. It’s less intrusive to the integrity of the walls than other methods and the breathable heritage putty allows for the correct wall expansion.
The size, location, and exposure of the gaps, as well as the infill panels composition, will dictate how to fill the gaps. Traditional lime-putty mortars with horse or badger hair are a good filler option, as they’re compatible with lime-based panels.
Even though it seems a simple technique, gap filling needs to be carried out by specialist builders, as traditional lime-putty mortar can be harmful to your health.
Replacing Infill Panels In Timber Frame Walls
If you need to remove infill panels to carry out structural repairs, you can replace them with pre-insulated panels. This is a quick, easy, affordable, and sustainable insulation option which, if done well, is likely to gain LPA approval.
Anske recommends using 50mm to 150mm pre-insulated wood-fibre batts made of natural timber, or hemp insulation batts.
Installing Insulation Between The Frame
Another suitable option to improve a historic building’s energy efficiency is adding insulation within the frame in rendered and clad elevations.
Adding Insulation To Rendered Elevations
If a render is in poor condition and needs to be replaced, you can add insulation within the timber frame, under the render. This is an effective method that is likely to be approved by the LPA. However, if cement based render has been used in the past, remedial works will be required.
Anske recommends using a like-for-like lime-putty, or earth-based, render to create a barrier against draughts, as it’s breathable, durable, and easy to obtain. In some cases, for example with medieval buildings, you might need to use a matching render which contains a cob mixture with natural elements, such as horse or badger hair, earth, and manure. Only a specialist will be able to identify the correct materials to use.
Adding Insulation To Clad Elevations
Repairing tile-hanging or weatherboarding offers an opportunity to add insulation within the thickness of the timber frame. This technique consists of installing a vapour barrier, like a Thermafleece breathable membrane, under the cladding. According to Aske, this is an effective and widely accepted method.
Installing Insulation Outside And Between The Frame
Adding external insulation is the most effective way to improve the thermal performance of a timber-framed wall. It entails installing wood-fibre boards over the exterior timber frame wall.
While the panels will make the exterior wall thicker, Anske says a good heritage specialist can ensure the changes are acceptable to the LPA.
Adding Insulation Inside The Frame
Installing insulation inside the frame is an effective way to upgrade the energy efficiency of a timber-framed building. This technique reduces the size of the room and alters the look of the internal wall. However, if done with the right application and materials, it stands a fair chance of gaining approval.
To achieve the best results, Aske often chooses Thermafleece lamb’s wool insulation or wood-fibre insulated batts, depending on the U-value of the panels and the size of the space that needs insulating.
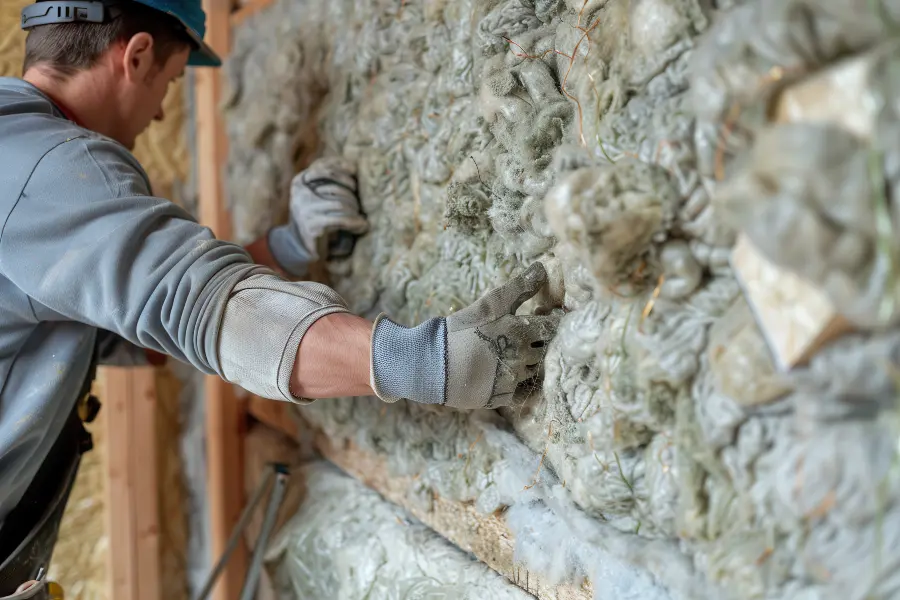
Insulating A Listed Building’s Walls
In principle, adding insulation to a listed building is possible and can be done cost-effectively. However, it requires careful design and good detailing, suitable choice of materials, and first-rate workmanship standards. Well-intentioned inapt changes can worsen the thermal performance of a structure.
That’s why you need to hire a specialist architect who can identify suitable options based on the building’s history, construction, environmental context, and more. They will then oversee the works to ensure specialist builders follow the condition of listed building consent set by the LPA.
Anske, our Heritage Consultant, has vast experience in improving the energy efficiency of listed buildings. He works at the James Clague offices in Canterbury and Tunbridge Wells, covering Kent, Sussex, Surrey, and the South East. You can request an initial consultation with Anske by contacting him here or calling 01227 649073.
For more information on upgrading the thermal performance of a listed building, read Historic England’s guides.
We offer a free consultation to help assess what you're trying to achieve, how we can help and explain the process.
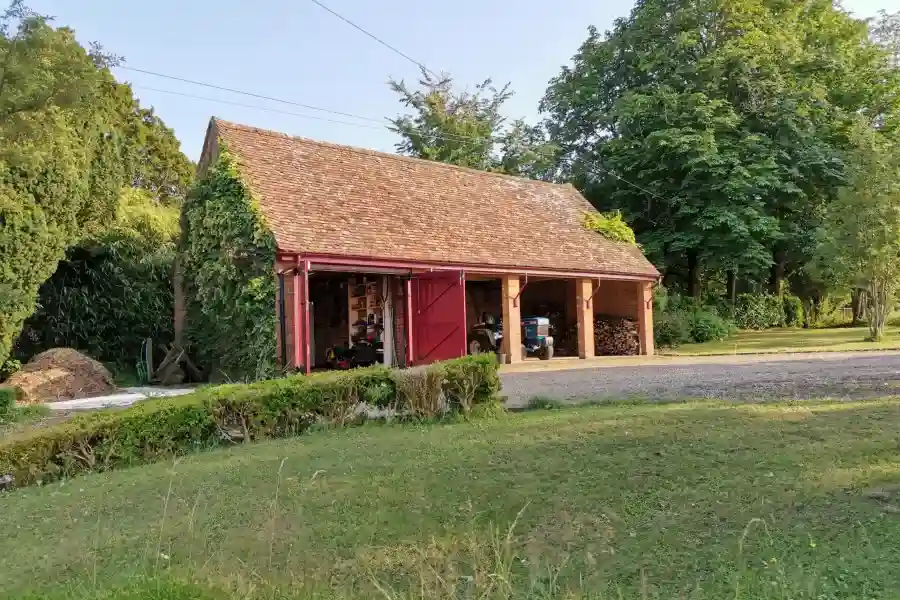
Permitted Development Rights In Conservation Areas: What Work Can You Do?
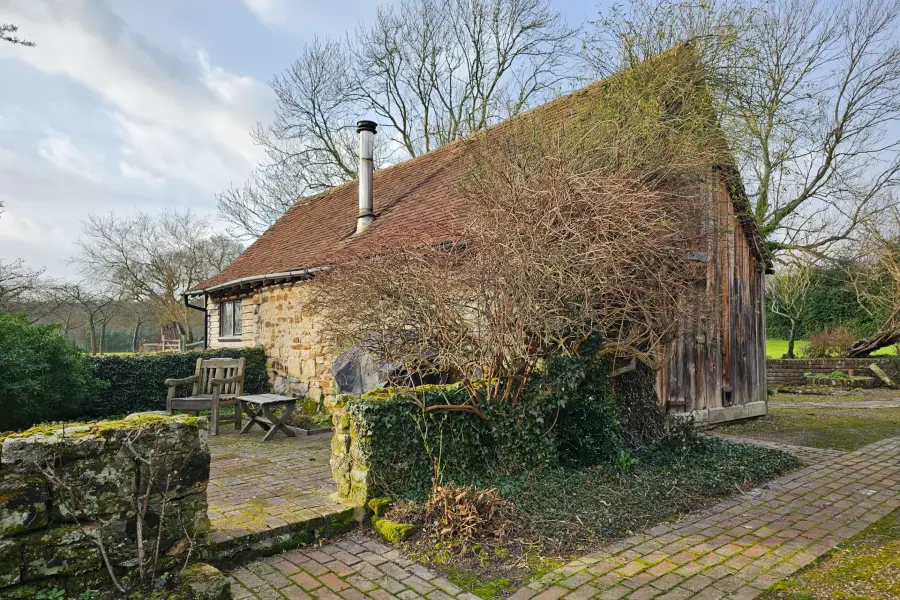
Is Your Outbuilding Curtilage-Listed? Here’s Everything You Need To Know
Our team of specialist architects offer a completely free and no-obligation telephone consultation to discuss your project, explain the process and how we can help.
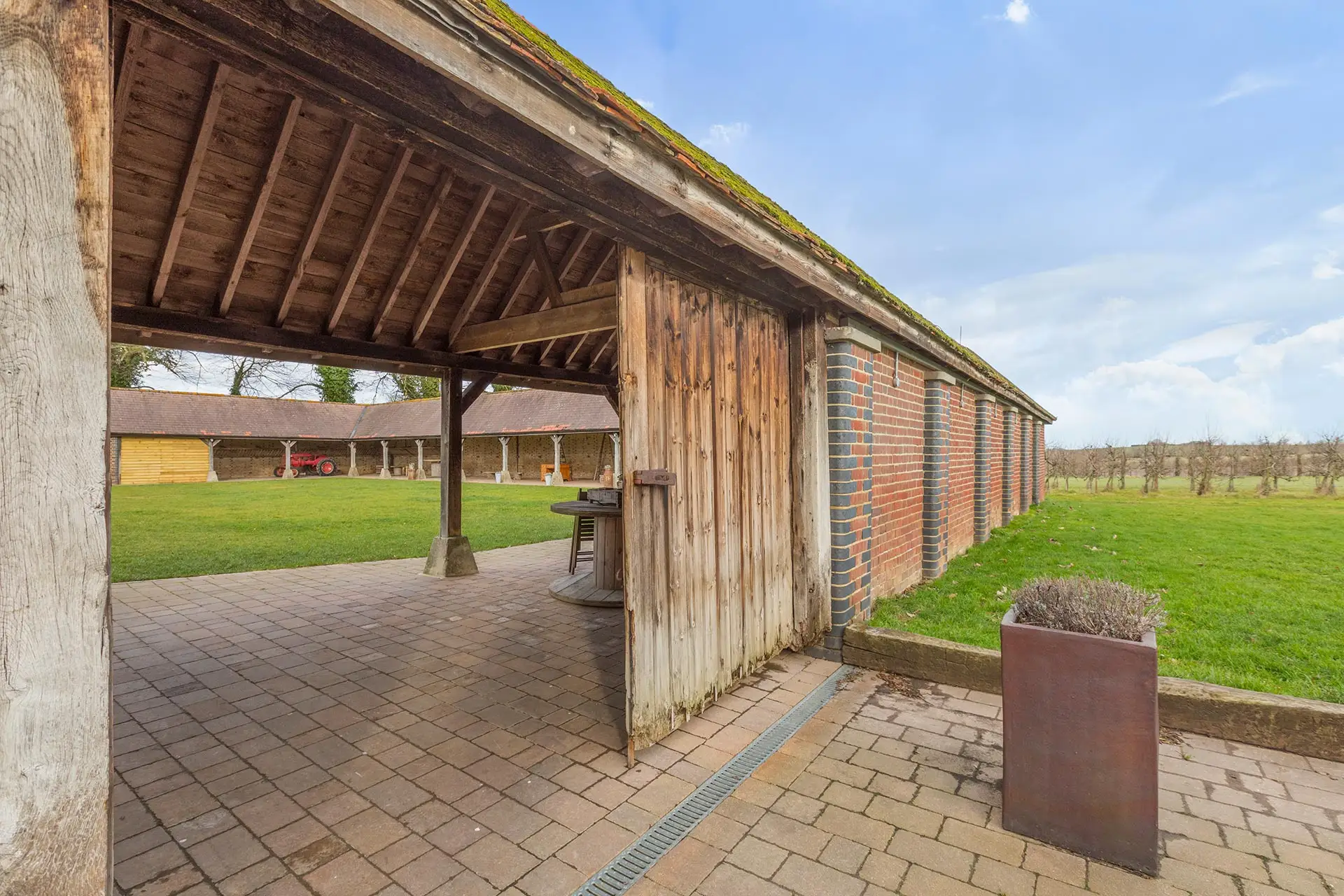